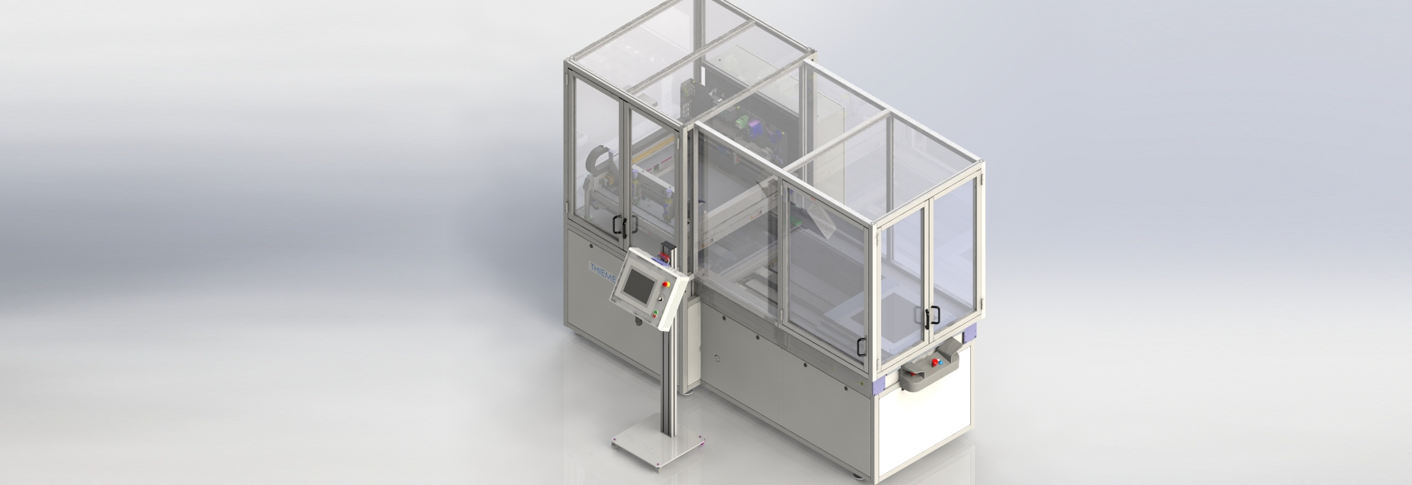
Fuel Cells from a Printer
Published at 07.01.2020
THIEME Fuel Cell Printing Platform
THIEME’s Fuel Cell Printing Platform can produce fuel cell stacks reliably and efficiently in a highly productive printing process.
The fuel cell is a key component of the renewable energy ecosystem. Printing machine manufacturer THIEME has developed an elegantly engineered machine platform for producing fuel cell stacks that lets users easily scale up their specific process requirements to serial production.
Electromobility is finally getting underway – as is demand for electric drive systems. One particularly promising power source is the fuel cell, which appears ideal for heavy vehicles and long distances. In fact, leading automotive suppliers believe that fuel cells could power up to 20 percent of all electric vehicles by 2030. However, the fuel cell shines as a key technology of the future in other applications as well, such as heating buildings.
Like a battery, a fuel cell is made of several layers. Several cells connected in series usually form a stack. Individual layers – such as insulating layers or membranes – can be produced very effectively by screen-printing a functional coating onto a substrate. The benefits are impressive: the printing process is much faster than other procedures while offering high precision and repeat accuracy.
“Our Fuel Cell Printing Platform gives customers a perfect mechanical basis for production,” said Nicolas Jahr from Thieme’s sales team, describing the benefits of this compact system that can be customized and expanded for each customer. Available options include variable print position, stencil printing, an antidrip unit and camera-guided automatic substrate alignment. The printing table’s travel path can be sized as needed depending on the chosen options. All printing parameters are monitored and controlled using a Siemens touch panel control unit.
From lab to fab
The system can also be outfitted with external components such as UV drying, plasma activation, deposit thickness measurement, automatic printing paste supply unit, automatic feeders and stackers, and a quality control system. The printing platform can thus be expanded one step at a time until it is a fully automated production line, potentially with robotic loading, in order to scale up product development to serial production.
“Thieme’s unique strength is designing production equipment to suit customer requirements,” Jahr said. “We don’t supply off-the-shelf printing machines but offer customers maximum flexibility. This is particularly important in cutting-edge fields like fuel cell production since processes can vary significantly from one manufacturer to the next. No other commercial printing system of this kind gives users so many options.”
Users benefit from Thieme’s long-standing experience in fuel cell printing: “We began the journey of realizing a fuel cell printing machine back in 2001,” said Dietmar Weber, Design Manager at Thieme, “and this machine is still used for small series production.” According to Weber, the new machine platform was designed based on experience gathered in eight relevant customer projects. “The insights we gained were invaluable in developing our fuel cell printing platform, which, technologically, is an entirely new machine.”