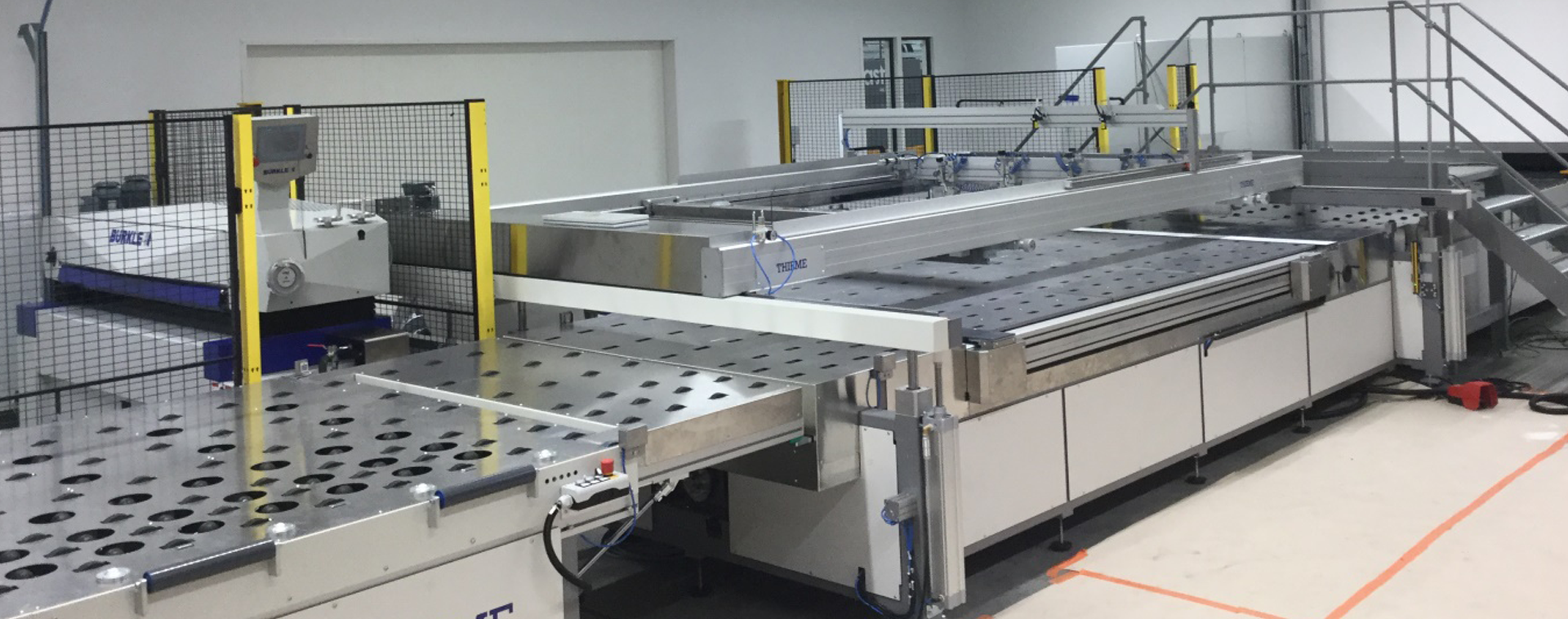
New screen printing line for architectural glass with highest possible flexibility and automation
Published at 04.02.2021
Thieme has installed a new printing line at LUMON Oy in Kouvola, Finland which allows an automatic adaptation of different glass sizes to be printed without screen change or manual cleaning.
One of the biggest issues with screen printing on architectural glass is the constant change of the glass dimension combined with holes in different location. A typical printing job is a full cover print with edging ink. But how to do that economically if the glass size is constantly changing and some glass have holes and some don´t?
Now we found a solution to overcome this problem. The new THIEME 3000 GS LS architectural printing machine can automatically measure the glass panel length and position the glass against the front mask. It is also aligning the travel length of the squeegee and flood coater automatically. This means that the printing is fully automated, but what about the areas in the screen where no ink could have been transferred to the glass because of holes and cut outs in the glass, or what about if a glass with a small width is processed than the printing area is set up for ? This has been considered by adding an intermediate paper printing station behind the printer. The print head can move backwards over the cleaning station after each print to perform a clean print onto paper which is fed from a roll to remove all unused ink in the defined printing area.
And the machine can even do more. Equipped with a programmable front mask it can print stripes in different position on the glass by entering the off-set from the glass edge in the operator panel (HMI) and the rest is done by the machine itself.
Flexible workflow
The HMI has a new flexible workflow which allows the operator to select the condition for each printing step individually. He can decide for example if the panel is transported automatically into the printing machine or started by the food paddle. This flexible workflow also includes functions like glass alignment, printing, glass inspection after the print and the out transport of the printed glass.
With this new flexibility the operators can optimize the workflow of each printing job.
Printing quality and inspection
After the printing the print head is moving away from the glass to the back allowing the operator to inspect the glass. It also gives him the opportunity to remove any dust particles in the print and to start a re-print to cover those areas again with ink.
The printing line with a maximum glass size of 1600 x 3000 mm is built for midsize applications like internal wall separators, shower cabins, balcony glassing, furniture glass etc. but the system can also be adapted to large size architectural glass with up to 3200 x 6000 mm.
The supplied printing line is accomplished with a roller coater from company Bürkle.
This new THIEME 3000 GS LS printing machine is the most flexible printing system on the market. It allows a fast set up and guaranties a high productivity for small and large printing jobs even with changing glass sizes.
The Thieme print head with double sided anti-drip function in combination with the high precision print base with hard anodized printing table fulfills the highest printing quality requirements.
This printing line is bringing screen printing to the next decade.